เทคโนโลยีพร้อมถ่ายทอด
ชื่อ
เครื่องต้นแบบผลิตเชื้อเพลิงเอทานอลขนาดเล็ก
ชม 2,142 ครั้ง
61
เจ้าของ
ผศ.ดร. อภิชาติ บุญทาวัน
เมล์
lamdaunxyz@hotmail.com
รายละเอียด
ผศ.ดร. อภิชาติ บุญทาวัน อาจารย์ประจำสาขาวิชาเทคโนโลยีชีวภาพ สำนักวิชาเทคโนโลยีการเกษตร มหาวิทยาลัยเทคโนโลยีสุรนารี (มทส.) สร้างเครื่องต้นแบบสำหรับการผลิตเชื้อเพลิงเอทานอลขนาดเล็กเป็นผลสำเร็จ มีประสิทธิภาพสูงใกล้เคียงกับการผลิตเชิงอุตสาหกรรม โดยสามารถผลิตเชื้อเพลิงเอทานอล หรือ E100 จากกากน้ำตาลและมันสำปะหลังได้สูงสุดถึง 30 ลิตรต่อวัน สามารถเติมในเครื่องยนต์ทางการเกษตรที่ใช้น้ำมันเบนซินและรถยนต์ที่ใช้น้ำมัน E85 มุ่งส่งเสริมการผลิตเชื้อเพลิงหมุนเวียนใช้ในชุมชน
เครื่องต้นแบบดังกล่าว เป็นหอกลั่นประสิทธิภาพสูงแบบต่อเนื่องมีการออกแบบระบบการกลั่นให้มีประสิทธิภาพในการแยกสารที่สูงมาก ซึ่งจากการทดสอบการกลั่นเอทานอลจากน้ำหมักจากกากน้ำตาล (molasses) สามารถกลั่นเอทานอลความเข้มข้นสูงสุดได้ถึงร้อยละ 93.00 ซึ่งใกล้เคียงกับความเข้มข้นสูงสุดที่สามารถกลั่นได้ในระดับอุตสาหกรรมซึ่งกลั่นได้ร้อยละ 95.0 และเมื่อผ่านขั้นตอนขบวนการกำจัดน้ำในส่วนกลั่นเพื่อผลิตเป็นเชื้อเพลิงเอทานอลจะสามารถผลิตเอทานอลเข้มข้นถึงร้อยละ 99.85 หรือ E 100 มีอัตราการกลั่นสูงสุดได้ถึง 30 ลิตรต่อวัน และสามารถนำเอทานอลที่ได้มาประยุกต์ใช้งานได้กับเครื่องยนต์เบนซิน อาทิ รถจักรยานยนต์ เครื่องตัดหญ้า เครื่องสูบน้ำ รถยนต์นั่งส่วนบุคคล รวมทั้งเป็นส่วนผสมสำหรับน้ำมันไบโอดีเซล
หลักการทำงานของเครื่องผลิตเชื้อเพลิงเอทานอลขนาดเล็ก แบ่งการทำงานออกเป็น 3 ส่วน ประกอบด้วย
1. การหมัก
2. การกลั่นลำดับส่วน
3. การแยกน้ำออกจากเอทานอลเพื่อผลิตเป็นเชื้อเพลิง
โดยขั้นตอนแรก คือ การหมัก สามารถใช้วัตถุดิบทางการเกษตรได้หลายอย่าง อาทิ กากน้ำตาล มันสำปะหลัง ข้าวฟ่างหวาน เป็นต้น
การทดลองนี้ได้ออกแบบขนาดถังหมักให้มีความจุ 250 ลิตร โดยจะทำการหมักกากน้ำตาลหรือ molasses จำนวน 60 กิโลกรัม ผสมกับน้ำจำนวน 220 ลิตร ทำการหมักกับยีสต์ จำนวน 1 กิโลกรัม เป็นเวลา 3 วัน ซึ่งในกระบวนการนี้จะได้เอทานอล 10 % (มีเอทานอล 10 ส่วน และน้ำ 90 ส่วน) จากนั้นจะนำไปสู่ขั้นตอนที่สอง การกลั่น เอทานอล โดยอุปกรณ์ที่ใช้ในขั้นตอนนี้เรียกว่าหอกลั่นลำดับส่วน โดยทั่วไปแล้วหอกลั่นในระบบอุตสาหกรรมจะมีลักษณะเป็นหอสูงภายในจะมีลักษณะเป็นแบบชั้น ๆ โดยจำนวนชั้นที่จะทำการกลั่นเอทานอลให้ได้ความบริสุทธิ์สูงสุดนั้น จะต้องมีจำนวนมากกว่า 75 ชั้น ส่งผลกระทบให้มีการลงทุนที่สูงควบคู่ไปกับการใช้ความร้อนสูงในการกลั่น แต่หอกลั่นประสิทธิภาพสูงแบบต่อเนื่องที่ได้ทำการพัฒนาขึ้น ได้มีการออกแบบระบบการกลั่นให้มีประสิทธิภาพในการแยกสารที่สูงมาก
ภายในหอกลั่นจะมีลักษณะเป็นท่อกลวง และมีการเพิ่มระบบการปั่นผสมไอด้วยใบพัดที่อยู่ภายในหอกลั่น เพื่อทำให้เกิดความเป็นเนื้อเดียวกัน โดยน้ำหมักจะถูกทำให้ร้อนและถูกป้อนเข้า ณ จุดกึ่งกลางของหอกลั่น โดยที่เอทานอลจะแยกตัวลอยขึ้นด้านบน โดยไอร้อนที่ลอยขึ้นมาจะถูกใบพัด พัดให้เข้ากับผนังด้านในของท่อหอกลั่น ทำให้เกิดการควบแน่นบางส่วน ในขณะที่ไอร้อนที่ถูกพัดตามมาจากด้านล่างจะทำให้เกิดการระเหยของของเหลวเพิ่มขึ้น และเกิดการผสมกันระหว่างไอและของเหลว ทำให้เกิดสมดุลระหว่างการควบแน่นและการกลายเป็นไอที่รวดเร็ว ส่งผลให้เกิดการแยกที่สมบูรณ์ภายในหอกลั่น
จากการทดสอบการกลั่นเอทานอลจากน้ำหมักด้วยระบบการป้อนแบบต่อเนื่องที่ได้ประดิษฐ์ขึ้นนี้ พบว่าสามารถกลั่นเอทานอลความเข้มข้นสูงสุดได้ถึงร้อยละ 93.0 โดยน้ำหนัก ซึ่งใกล้เคียงกับความเข้มข้นสูงสุดที่สามารถกลั่นได้ในระดับอุตสาหกรรม (ร้อยละ95.0) จากนั้นจึงนำเข้าสู่ขั้นตอนที่สามคือการกำจัดน้ำในส่วนกลั่นเพื่อผลิตเป็นเชื้อเพลิง เอทานอล ทั้งนี้เนื่องจากการกลั่นลำดับส่วนแบบปกติ จะไม่สามารถที่จะแยกน้ำออกสารละลายเอทานอลได้ทั้งหมด (โดยความเข้มข้นสูงสุดของเอทานอลที่สามารถทำการกลั่นได้นั้น จะอยู่ที่ร้อยละ 95 โดยน้ำหนัก)
สำหรับเทคโนโลยีการกำจัดน้ำในงานวิจัยนี้ มีชื่อเรียกว่าการแยกไอผ่านเยื่อแผ่น หรือ vapor permeation โดยเยื่อแผ่นชนิดนี้จะยอมให้น้ำผ่านได้ดีกว่าเอทานอล โดยวัสดุที่ใช้ในการขึ้นรูปสำหรับงานวิจัยชิ้นนี้ได้เลือกใช้เยื่อแผ่นชนิดเซรามิก (ceramic membrane) ซึ่งมีความคงตัวเชิงกลที่สูงมาก โดยสามารถทำให้มีขนาดของ รูพรุนประมาณ 3 อังสตรอม (1 อังสตรอมมีขนาดเท่ากับ 10-10 เมตร) ซึ่งจะทำให้สามารถแยกน้ำออกจากเอทานอลได้อย่างมีประสิทธิภาพ (โดยน้ำจะมีขนาดโมเลกุล 2.6 อังสตรอม ในขณะที่เอทานอลมีขนาดโมเลกุล 4.4 อังสตรอม)
หลักการทำงานของระบบการแยกไอผ่านเยื่อแผ่นนั้น จะทำการปั๊มสารละลายเอทานอลที่ได้จากการกลั่นผ่านเครื่องแลกเปลี่ยนความร้อน เพื่อทำให้สารละลายเอทานอลอยู่ในสภาวะที่เป็นก๊าซร้อน โดยจะมีอุณหภูมิที่ 140 องศาเซลเซียส และมีความดันประมาณ 4 บรรยากาศ เมื่อไอของสารละลายเอทานอลเคลื่อนที่ผ่านผิวหน้าของเยื่อแผ่นดังกล่าว โมเลกุลของน้ำจะถูกดูดซับไว้ที่ผิวหน้าของเยื่อแผ่นก่อนที่จะเคลื่อนที่ทะลุผ่านเยื่อแผ่นออกไป ส่วนโมเลกุลของเอทานอลซึ่งมีขนาดใหญ่กว่าขนาดของรูพรุนของเยื่อแผ่น จะเคลื่อนที่ไปตามผิวหน้าของเยื่อแผ่นและจะมีความเข้มข้นเพิ่มขึ้นเรื่อย ๆ จนกระทั่งหลุดออกจากระบบเป็นเชื้อเพลิงเอทานอล 100 % หรือ E100 นั่นเอง
สำหรับชุดอุปกรณ์ต้นแบบ เหมาะสำหรับการส่งเสริมให้ประชาชนทั่วไป ได้ใช้ในรูปของโรงงานผลิตเชื้อเพลิง ขนาดเล็กสำหรับชุมชน โดยอาจจัดตั้งเป็นระบบสหกรณ์เชื้อเพลิงสำหรับชุมชน เพื่อส่งเสริมในการประยุกต์ใช้เชื้อเพลิงเอทานอลสำหรับเครื่องยนต์เบนซิน และยังสามารถใช้เอทานอลดังกล่าวเป็นส่วนประกอบหลักในการผลิต ไบโอดีเซลแบบครบวงจร ซึ่งจากขบวนการผลิตเอทานอลดังกล่าวจะมีต้นทุนการผลิตอยู่ที่ 20 - 25 บาทต่อลิตร โดยชุดอุปกรณ์ต้นแบบดังกล่าวใช้งบประมาณในการผลิตประมาณ 500,000 บาท
เครื่องต้นแบบดังกล่าว เป็นหอกลั่นประสิทธิภาพสูงแบบต่อเนื่องมีการออกแบบระบบการกลั่นให้มีประสิทธิภาพในการแยกสารที่สูงมาก ซึ่งจากการทดสอบการกลั่นเอทานอลจากน้ำหมักจากกากน้ำตาล (molasses) สามารถกลั่นเอทานอลความเข้มข้นสูงสุดได้ถึงร้อยละ 93.00 ซึ่งใกล้เคียงกับความเข้มข้นสูงสุดที่สามารถกลั่นได้ในระดับอุตสาหกรรมซึ่งกลั่นได้ร้อยละ 95.0 และเมื่อผ่านขั้นตอนขบวนการกำจัดน้ำในส่วนกลั่นเพื่อผลิตเป็นเชื้อเพลิงเอทานอลจะสามารถผลิตเอทานอลเข้มข้นถึงร้อยละ 99.85 หรือ E 100 มีอัตราการกลั่นสูงสุดได้ถึง 30 ลิตรต่อวัน และสามารถนำเอทานอลที่ได้มาประยุกต์ใช้งานได้กับเครื่องยนต์เบนซิน อาทิ รถจักรยานยนต์ เครื่องตัดหญ้า เครื่องสูบน้ำ รถยนต์นั่งส่วนบุคคล รวมทั้งเป็นส่วนผสมสำหรับน้ำมันไบโอดีเซล
หลักการทำงานของเครื่องผลิตเชื้อเพลิงเอทานอลขนาดเล็ก แบ่งการทำงานออกเป็น 3 ส่วน ประกอบด้วย
1. การหมัก
2. การกลั่นลำดับส่วน
3. การแยกน้ำออกจากเอทานอลเพื่อผลิตเป็นเชื้อเพลิง
โดยขั้นตอนแรก คือ การหมัก สามารถใช้วัตถุดิบทางการเกษตรได้หลายอย่าง อาทิ กากน้ำตาล มันสำปะหลัง ข้าวฟ่างหวาน เป็นต้น
การทดลองนี้ได้ออกแบบขนาดถังหมักให้มีความจุ 250 ลิตร โดยจะทำการหมักกากน้ำตาลหรือ molasses จำนวน 60 กิโลกรัม ผสมกับน้ำจำนวน 220 ลิตร ทำการหมักกับยีสต์ จำนวน 1 กิโลกรัม เป็นเวลา 3 วัน ซึ่งในกระบวนการนี้จะได้เอทานอล 10 % (มีเอทานอล 10 ส่วน และน้ำ 90 ส่วน) จากนั้นจะนำไปสู่ขั้นตอนที่สอง การกลั่น เอทานอล โดยอุปกรณ์ที่ใช้ในขั้นตอนนี้เรียกว่าหอกลั่นลำดับส่วน โดยทั่วไปแล้วหอกลั่นในระบบอุตสาหกรรมจะมีลักษณะเป็นหอสูงภายในจะมีลักษณะเป็นแบบชั้น ๆ โดยจำนวนชั้นที่จะทำการกลั่นเอทานอลให้ได้ความบริสุทธิ์สูงสุดนั้น จะต้องมีจำนวนมากกว่า 75 ชั้น ส่งผลกระทบให้มีการลงทุนที่สูงควบคู่ไปกับการใช้ความร้อนสูงในการกลั่น แต่หอกลั่นประสิทธิภาพสูงแบบต่อเนื่องที่ได้ทำการพัฒนาขึ้น ได้มีการออกแบบระบบการกลั่นให้มีประสิทธิภาพในการแยกสารที่สูงมาก
ภายในหอกลั่นจะมีลักษณะเป็นท่อกลวง และมีการเพิ่มระบบการปั่นผสมไอด้วยใบพัดที่อยู่ภายในหอกลั่น เพื่อทำให้เกิดความเป็นเนื้อเดียวกัน โดยน้ำหมักจะถูกทำให้ร้อนและถูกป้อนเข้า ณ จุดกึ่งกลางของหอกลั่น โดยที่เอทานอลจะแยกตัวลอยขึ้นด้านบน โดยไอร้อนที่ลอยขึ้นมาจะถูกใบพัด พัดให้เข้ากับผนังด้านในของท่อหอกลั่น ทำให้เกิดการควบแน่นบางส่วน ในขณะที่ไอร้อนที่ถูกพัดตามมาจากด้านล่างจะทำให้เกิดการระเหยของของเหลวเพิ่มขึ้น และเกิดการผสมกันระหว่างไอและของเหลว ทำให้เกิดสมดุลระหว่างการควบแน่นและการกลายเป็นไอที่รวดเร็ว ส่งผลให้เกิดการแยกที่สมบูรณ์ภายในหอกลั่น
จากการทดสอบการกลั่นเอทานอลจากน้ำหมักด้วยระบบการป้อนแบบต่อเนื่องที่ได้ประดิษฐ์ขึ้นนี้ พบว่าสามารถกลั่นเอทานอลความเข้มข้นสูงสุดได้ถึงร้อยละ 93.0 โดยน้ำหนัก ซึ่งใกล้เคียงกับความเข้มข้นสูงสุดที่สามารถกลั่นได้ในระดับอุตสาหกรรม (ร้อยละ95.0) จากนั้นจึงนำเข้าสู่ขั้นตอนที่สามคือการกำจัดน้ำในส่วนกลั่นเพื่อผลิตเป็นเชื้อเพลิง เอทานอล ทั้งนี้เนื่องจากการกลั่นลำดับส่วนแบบปกติ จะไม่สามารถที่จะแยกน้ำออกสารละลายเอทานอลได้ทั้งหมด (โดยความเข้มข้นสูงสุดของเอทานอลที่สามารถทำการกลั่นได้นั้น จะอยู่ที่ร้อยละ 95 โดยน้ำหนัก)
สำหรับเทคโนโลยีการกำจัดน้ำในงานวิจัยนี้ มีชื่อเรียกว่าการแยกไอผ่านเยื่อแผ่น หรือ vapor permeation โดยเยื่อแผ่นชนิดนี้จะยอมให้น้ำผ่านได้ดีกว่าเอทานอล โดยวัสดุที่ใช้ในการขึ้นรูปสำหรับงานวิจัยชิ้นนี้ได้เลือกใช้เยื่อแผ่นชนิดเซรามิก (ceramic membrane) ซึ่งมีความคงตัวเชิงกลที่สูงมาก โดยสามารถทำให้มีขนาดของ รูพรุนประมาณ 3 อังสตรอม (1 อังสตรอมมีขนาดเท่ากับ 10-10 เมตร) ซึ่งจะทำให้สามารถแยกน้ำออกจากเอทานอลได้อย่างมีประสิทธิภาพ (โดยน้ำจะมีขนาดโมเลกุล 2.6 อังสตรอม ในขณะที่เอทานอลมีขนาดโมเลกุล 4.4 อังสตรอม)
หลักการทำงานของระบบการแยกไอผ่านเยื่อแผ่นนั้น จะทำการปั๊มสารละลายเอทานอลที่ได้จากการกลั่นผ่านเครื่องแลกเปลี่ยนความร้อน เพื่อทำให้สารละลายเอทานอลอยู่ในสภาวะที่เป็นก๊าซร้อน โดยจะมีอุณหภูมิที่ 140 องศาเซลเซียส และมีความดันประมาณ 4 บรรยากาศ เมื่อไอของสารละลายเอทานอลเคลื่อนที่ผ่านผิวหน้าของเยื่อแผ่นดังกล่าว โมเลกุลของน้ำจะถูกดูดซับไว้ที่ผิวหน้าของเยื่อแผ่นก่อนที่จะเคลื่อนที่ทะลุผ่านเยื่อแผ่นออกไป ส่วนโมเลกุลของเอทานอลซึ่งมีขนาดใหญ่กว่าขนาดของรูพรุนของเยื่อแผ่น จะเคลื่อนที่ไปตามผิวหน้าของเยื่อแผ่นและจะมีความเข้มข้นเพิ่มขึ้นเรื่อย ๆ จนกระทั่งหลุดออกจากระบบเป็นเชื้อเพลิงเอทานอล 100 % หรือ E100 นั่นเอง
สำหรับชุดอุปกรณ์ต้นแบบ เหมาะสำหรับการส่งเสริมให้ประชาชนทั่วไป ได้ใช้ในรูปของโรงงานผลิตเชื้อเพลิง ขนาดเล็กสำหรับชุมชน โดยอาจจัดตั้งเป็นระบบสหกรณ์เชื้อเพลิงสำหรับชุมชน เพื่อส่งเสริมในการประยุกต์ใช้เชื้อเพลิงเอทานอลสำหรับเครื่องยนต์เบนซิน และยังสามารถใช้เอทานอลดังกล่าวเป็นส่วนประกอบหลักในการผลิต ไบโอดีเซลแบบครบวงจร ซึ่งจากขบวนการผลิตเอทานอลดังกล่าวจะมีต้นทุนการผลิตอยู่ที่ 20 - 25 บาทต่อลิตร โดยชุดอุปกรณ์ต้นแบบดังกล่าวใช้งบประมาณในการผลิตประมาณ 500,000 บาท
คำสำคัญ
บันทึกโดย
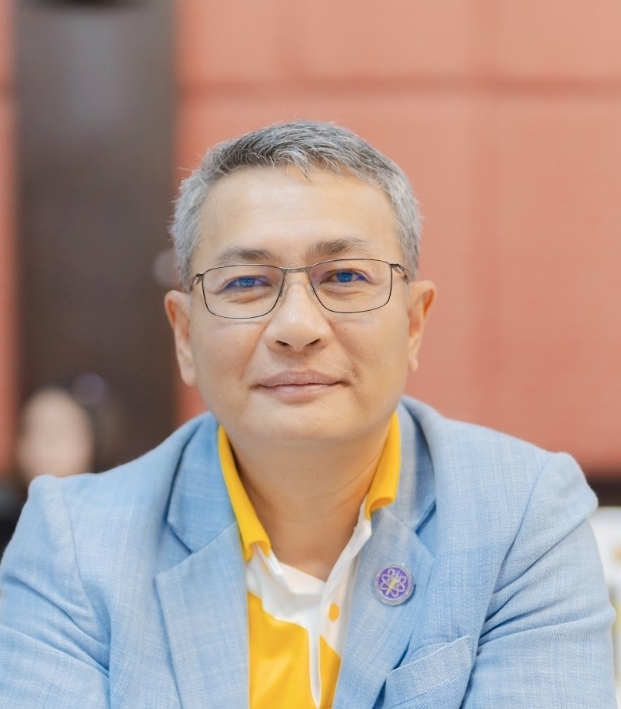